There are a few factors to be considered when determining the proper wall thickness for a low volume injection molding; it must obtain an equilibrium between the correct product weight, carefully calculated design and reasonable financial allocation. In particular, a plastic product with thick walls allows greater durability, however it has a greater likelihood of warping during the cooling stage of the manufacturing operation. As one of the design elements within the industry of plastic manufacturer injection, wall thickness has the greatest influence on the overall quality, speed of manufacturing process, and the operational cost of an item. In this article, we will talk about its importance in the overall success of a manufacturing venture. This is the Perks of Uniform Wall ThicknessAlthough walls with a thicker thickness offer greater durability, there are certain advantages to manufacturing thin walls. As a matter of fact, more time is spent in manufacturing process, the more benefits can be acquired if wall thickness remains consistent light and thin. This is particularly relevant when it comes to manufacturing an elastic belt buckle hook as well as loop. This is also regarded to be crucial when projects require a large volume of output. A wall thickness that is suitable for your plastic products allows for:
Wall thickness isn’t tied to any limitations or constraints but, most of the time the aim is to create the tiniest wall that is possible, considering the structure’s size the geometry, dimensions, and other requirements. The raw material qualities and the flow characteristics should be taken into account by the moulding company during this crucial phase. The Effects of Improper Wall ThicknessDuring the cooling phase of polycarbonate injection molding manufacturing, uniform wall thickness is crucial. If certain parts in the item are less than the rest, the region could be susceptible to warping, twisting, cracking, or collapse. That will certainly alter the appearance of the belt buckle you are making. A proper ABS injection molding wall thickness can reduce the chances of residual stress and shrinkage of the completed product. If a consistent wall thickness is not feasible, gradually increasing the thickness is a good alternative to consider. The appropriate wall thickness of a product supports a uniform circulation of the raw material through the molds, which guarantees an optimal injection molding process. Different wall thicknesses will result in the liquified material to choose a particular route that could result in undesirable outcomes like weld lines, filled that is not balanced or air trapped. |
https://www.plasticmoulds.net/low-volume-production |
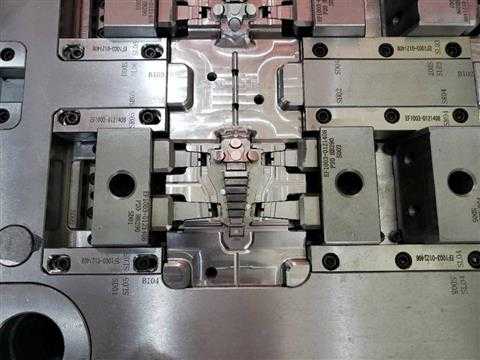